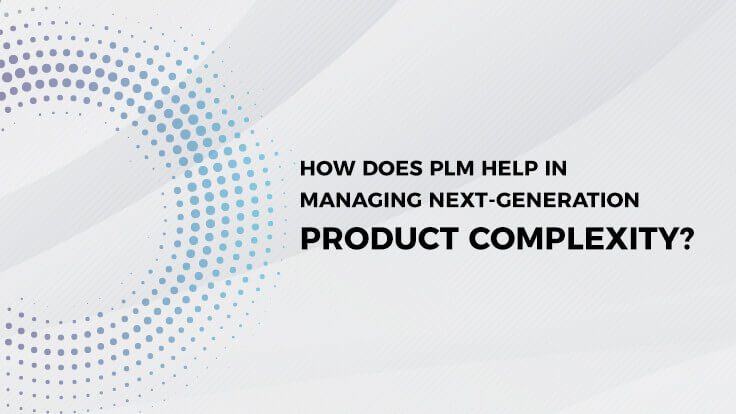
The simple reality of 21st centuryâs products is that they are highly complex. Complex to design, complex to produce and also complex to support. Across the manufacturing sector, the trend over the last decade has especially been: âincreased complexityâ. Rise in Complexity: No Simple Products Complexity is a consequence of increased product variability. Over many decades, there has been a striking rise in the product variability due to several factors like market demands, product /process variety, technical complexity, corporate strategy, consumer demands, competition pressure and financial constraints.
For instance, until hardly a few years back, the gearbox in a car was merely a mechanical assembly without any involvement of software or electrical parts. However, with accelerated developments and rising product complexity, the present-day gearbox is designed and developed with electronic components, microcircuits and actuating drives while software governs everything. Just like a simple gearbox, the complexity has increased for most of the products in the last few decades.
âThe software has become a growing factor and governs almost every type of product today.â
Manufacturers are facing a new range of challenges with these innovations. Today, all the engineers (mechanical, software and electrical) must work collectively on the same product, regardless of their location across the globe. This implies that all these disciplines (mechanical, software and electrical) must be coordinated meticulously, which further makes the processes and projects way more sophisticated and complicated than they traditionally were. Besides this, manufacturers also have to assure the safety of their products at every stage- especially in industries like automotive and healthcare, where the lives of users can be at greater risk. Guaranteeing safety gets tricky when the product is still in production and even more when field updates are required, particularly for software.
Lastly, products are not the only thing growing in complexity. Complexity is not just a design issue. It concerns from product portfolio to product planning through manufacturing, service, and support. Compliance mandates also add to the complexity. Manufacturers, today, must work out their ways through a maze of rules and regulations to stay in compliance while avoiding critical business risks.Efficiently and effectively managing product complexity in every form poses a crucial business issue. Let us explore how PLM addresses the five most crucial dimensions of product complexity to attain maximum profitability. The dimensions include:
- Mechanical Complexity
- Mechatronics
- Global Markets
- Global Designs and Manufacturing
- Life cycle profitability
Current Challenges
1. Mechanical Complexity in Products
Today, even the simplest of the mechanical products have gone complex. Advancements in engineering have enabled engineers to design more functional products making them compact and cost-efficient. incorporation of advanced materials like nanomaterials and composites enforces innovation and increased flexibility, but in turn, introduces its own complexity challenges. Apart from this, advanced design techniques to promote reuse and agility further makes things more complex. Several manufacturers have now made a shift towards platform-based designs, where products share a common platform that is the base on which multiple other products will be built.Similarly, manufacturers are also engaging modular design techniques which comprise independent subsystems that can be interchanged further to meet specific requirements. The interfaces that are associated with the different modules are defined and managed to further ease the incorporation of the modules into multiple products. Thus, modularization and reuse are fresher concepts in the industry. It is absolutely a product complexity problem to keep track of everything.
In many ways, these new design approaches cut down complexity while improving reuse of parts and designs. But, at the same time, it also augments the complexity of design and configuration management processes. Savings in costs justify it, as does the capability to immediately introduce new changes or technologies across various products. This results in new challenges for engineers to manage modules and platforms which must work efficiently in multiple product scenarios.
One Size Does Not Fit All
Another challenge that relates to this is the rise in customization or personalization of products. Numerous manufacturers have initiated configurability into their products which will need final engineering based on order specifications. Even the product variants that are standard and pre-defined and provides multiple options to the customers need severe engineering rigor and control, after all, one size doesnât fit all.
2.Complexity beyond Mechanics – Mechatronics
Beyond mechanical complexity, manufacturers are involved in developing âsmarterâ products. Consider the connected devices. The Internet-of-Things (IoT) will barely leave any technical device unconnected, rendering everything âsmartâ. For instance, next-generation automobiles might have 40 or more microprocessors which would be managing everything from entertainment, to engine timing, to braking.
This combination of all three disciplines (mechanical, electrical and software), known as âmechatronicsâ has further added exponentially to the product complexity. And this complexity is only predicted to go beyond the product itself, as many devices like cell phones and navigation systems, in future, might be a part of larger systems with supplementary applications on various devices and servers, further increasing the complexity to networking and operating systems. For all of these products, each element must be designed independently.
What is of utmost importance is that each of the design disciplines must work cordially because all the elements of the product must be designed as a part of a system and compulsorily be kept in sync. Having and keeping designs in synchronization is a basic challenge. Many companies are stepping ahead leveraging simulation to validate products at a systems level as well as individual disciplines like mechanics. Simply put, the lack of integrated product configuration results in cost overruns, safety issues and delays due to faulty products.
The executive level should be aware of these issues for several reasons. One, because different product departments are not correctly connected, deficient communication between the hardware and the software engineers becomes a constant source of unaffordable errors which can conclude in a varied safety issue. This puts companies to liability risk which can directly harm business results.
Whatâs more to it? It can absolutely put real people in real danger. Who would have ever imagined that a firmware flaw could end up in accidental acceleration? Well, it certainly can and it actually did in one of the leading manufacturerâs cars with lethal consequences. In another case, a car manufacturer had to withdraw 145,000 cars due to software issues at a massive cost to both the companyâs balance sheet and of course its brand image.
3. Complexity in Globalization
Globalization has been one more factor that has complicated the product development. Manufacturers compete in global markets today which has caused increased cost pressure but have also opened up newer market opportunities. In the present global sphere, manufacturers largely compete for time-to-market on a global basis.
Today leading organizations are indulged in launching products in multiple markets at the same time or in accelerated succession instead of launching a product in one market and later localizing it. Product launches that are global are always challenging just as localization in multiple geographies is. This is because every market has varied criteria based on local preferences while being driven by local regulations.
Comprehending these requirements ahead in time helps organizations to optimize the number of product variants which are needed to meet multiple markets and empowers them to take platform approach while adding a layer of complexity. Globalization also impacts entire product lifecycle because, with it, usability and serviceability become major issues.
4. Complexity in Designs and Manufacturing
Besides products, globalization has largely impacted manufactures themselves. The present generation manufacturers are designing and developing products globally. Traditionally, product development sites were likely to be on one site, whereas in contrast to it, today the product development sites are spread across the globe. It has transformed the entire engineering community into a more virtual organization.
While global design approaches and centers of excellence are very important approaches, it demands additional efforts to keep all the diverse teams aligned and synchronized. Besides designs, globalization impacts production. Product designers continually find themselves crossing corporate boundaries besides physical ones; as manufacturers are keen on adopting expanding global supply chains to enjoy benefits of local talent and other cost benefits. This leads to increasing adoption of concurrent engineering strategies along with âdesign anywhere-build anywhereâ approach.
5. Complexity in Lifecycle Profitability
Besides all the complexities of product designs, companies are supposed to focus also on product lifecycle. Increasing amount of disconnected processes are paving ways to more collaborative approaches. The total profitability of a product across its lifecycle require greater involvement from the resources as the later stages of the lifecycle are critical to product profitability.
This implies that diverse organizational groups must be able to share product information in a quick and complete manner. In order to make quick higher fidelity decisions, product information must be easily available to people involved in the process. Or else, it may result in significant rework or can possibly cause issues with suboptimal designs. Manufacturers are taking up vital roles in services too. In many cases, this involvement is to perceive greater margins from services as globalization has brought the product prices down.
While in other cases, manufacturers indulge in various operation and service life cycles via SLAâs, paying for the product as a service or by performance-based contracts. Today, market demands have inclined to demand increasing accountability by the manufacturer as the warranty periods have increased.
Solution to the complexities â Resilient PLM Software
Today, several companies are learning their lessons the harder way that they cannot combat these challenges with their existing legacy PDM installations. They must take the new approach. All that they need is a new, resilient PLM solution to lead in their enterprise-wide digital transformation journey. A solution that is Flexible, Scalable and Upgradable.
PLM was originally developed with no petty promise than to transform the industrial production. PLM comprises of a wider approach to deployment and much higher level of integration across each phase of the product lifecycle, across different disciplines like mechanical, electrical and software, global locations and entire supply chain. The PLM processes are expected to cut down error rates and accelerate design, development, and manufacturing.
The ultimate goal of the PLM is to map the entire product lifecycle with a single, unified source of data for each and every processes and department including suppliers and other partners. PLMs are designed to centrally manage and track product requirements, product specifications, project plans- literally every department from design through acquisition to support. The benefits that are targeted from this are faster time-to-market, efficient use of budgets and reduced waste.
1. Flexible PLM Solution
Every business is distinct and is continually evolving. And, so a flexible PLM is a must. The conventional approach used in old PDM systems becomes unsuccessful here as the business logic, data model, services and database structures are thoroughly embedded in the source code. This results in a massive block of software which only an expert developer can access. So, for any change required by the business, the code has to be rewritten.
Today, with the model-based technology, the PLM can provide the necessary flexibility to your business; now and in future with adaptive data models, process models and other business rules. This implies that the business needs can be exactly met either by leveraging innovative applications which can be easily adapted or by customer-specific applications which can easily be developed.
For the companies to leverage the true potential and advantages of PLM, the implementations must be carried out quickly and should be able to keep pace with ever-evolving business needs. They must become agile. Though, the agile implementation can only be carried out when the basic PLM platform technology is equally adaptable to the methodology itself.
Legacy PDM systems fail to cater flexibility to go âagileâ. Whereas the PLM architecture facilitates agile implementation that shows tangible business results quickly. Implementation cycle times are much shorter with PLM than PDM systems which further cuts down costs and risks.
2. Scalable PLM Software
A PLM software has to have the capabilities to grow in line with the business requirements. Old PDM systems can be difficult to scale as different applications are typically developed on disparate platforms. This further adds complexity to support collaborative business processes as lone applications may operate in a silo or might even be poorly integrated with each other.
On the other hand, with the integrated applications running on a unified platform, it gets easier to scale PLM implementations while adding support for new disciplines, functions or new processes. In PLM software, scaling is further complemented by cross-application Visual Collaboration capabilities which empower users to review, markup and also comment on various 3D models, documents and other data in browser environment without needing access to original authoring tools.
Effortless collaboration in a secure environment within a global context and across global supply chains is thus made possible without any complications/hurdles with PLM.
3. Upgradeable PLM Software
Software upgrades can turn into great nightmares for companies. Major issue lies in the massive structure of legacy PDM systems which further makes it impossible to complete an upgrade without thorough updates to custom codes followed by testing and recertification. In contrast to PDMâs, PLM software can be easily upgraded with zero business downtime or risk of losing any vital feature and changes.
Our experience of PLM Software implementation To conclude, we have learned that designing, manufacturing and supporting complex, connected products pose major hindrances for organizations today. Besides IoT and smart devices, there has been a flourishing trend towards products as a service; which implies that many products wouldnât be sold anymore rather would be provided as a solution package, including support and services.
To facilitate this, more disciplines beyond mechanical 3D CAD will be participating throughout the lifecycle and will require working closely in an increasingly integrated fashion than they currently are. Besides this, manufacturers will have to concentrate more on coordinating their suppliers as they provide parts or entire assemblages with technology embedded in them. Also managing the Digital Twin and Digital Thread is going to be a mandate in the near future.
Several companies have already made sense of these challenges and have taken initiatives to drive their enterprise-wide digital transformation in product development. They have realized that only a resilient PLM platform will allow them to fully support the business of engineering.